Highlights
- In April 2011, Brand-Rex became the first structured cabling company to achieve PAS2060 Carbon Neutral status.
- Brand-Rex has reduced the carbon footprint of its global operations by 141 tonnes since 2009, despite increasing output by an extra 29 million metres of cable.
- Measures undertaken at the Glenrothes site include replacing fuel oil with natural gas, saving £78,000 in the first 12 weeks of 2011 alone.
- Changed the roofing panels to allow natural daylight into the factory, providing natural light and heating, which allows up to 1000 lights to be turned off during daylight hours
- Evidence of strong environmental commitment from senior management and the CEO enabling initiatives to be taken on board quickly.
- Development of a product to minimise energy generated and materials required for cables, reducing energy consumption required for cooling.
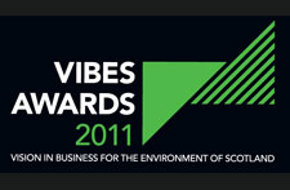
Brand-Rex is a leading global supplier of structured cabling systems for data networks. At their headquarters in Glenrothes, Brand-Rex primarily manufactures copper and fibre optic cables. In 2011, they became the first structured cabling company to achieve Carbon Neutral status to PAS2060.
Brand-Rex was selected as the winner of the Management Award in the Large Business Category for its entire life cycle approach to reducing its business impacts—from its raw materials through to the final product. The holistic approach shown by Brand-Rex has provided benefits to the business and also customers and the wider global community.
The commitment to reducing the impact of its products’ lifecycles was clearly demonstrated by the Brand-Rex global CO2 emissions offsetting project, which involves:
- using a methane-flaring plant in Chile—where 34% of world copper is mined—reducing greenhouse gas emissions and creating jobs in a developing country;
- using a hydropower plant in Turkey where the copper rod is manufactured, reducing emissions by displacing the need for fossil fuels and supporting a sustainable trout fishery on the banks of the river;
- using a Fuel Switch biomass project in Brazil, which directly offsets the companies Fossil Fuel emissions. This project replaces heavy oil with a sustainable biomass with the aim of reducing deforestation, and also employing disabled persons, thereby encouraging social inclusion.
The VIBES judges were also impressed by the Brand-Rex use of innovatively-designed cables which can be blown through ducting using compressed air technology. This removes the need to dig up them up to replace them, saving customers money at the outset, as they do not need to install too much capacity early on. It also saves money when upgrades are required because of the ease with which the cable can be installed. In addition, Brand-Rex created the smallest product for the zone datacentre market, reducing the company’s carbon footprint, reducing the amount of material required and contributing to a reduction in energy use to help customers work towards a green environment.
Brand-Rex has shown commitment to reducing the company carbon footprint by 20% by 2015 (versus 2009), exceeding the targets set by the Scottish and the UK governments, and achieving a 13% reduction in the first year! The company did this by increasing recycling from 10 tonnes in 2009 to 60 tonnes in 2010 and by replacing roof panels at the site with clear plastic panels to maximise natural light enabling around 900 lights to be turned off during daylight hours.
The VIBES panel found a unique selling point in Brand-Rex’ use of an innovative method of measuring the carbon footprint of each metre of cable: the company has reduced the carbon emissions relative to 1 metre of cable from 46.7g to 40.6g.
Brand-Rex has also undertaken an energy reduction project at the Glenrothes site, including:
- replacing panel lighting;
- removing fuel oil and replacing with it with natural gas, generating a 223 tonne CO2 emission saving. In order to generate the equivalent heating using fuel oil would have cost £95K for the first 12 weeks of 2011; instead, it cost £17K using the new gas heating system;
- PDF invoicing;
- improved transportation logistics (less airfreight, more sea freight);
- draft-proofing
- better water-management systems.
Without these programmes, the carbon footprint would have been 1324 tonnes higher for the same volume of production in 2009.
Future plans include removing redundant flues and chimneys so that the factory is better insulated thereby reducing heating needs, and investigating whether rainwater could be used to naturally cool the water supply. Brand-Rex is also working towards ‘Zero Waste’ and is investigating suitable renewable energy sources, as well as continuing to reduce the carbon footprint of its products.